Induktionslöten von Aluminium mit Computerunterstützung
Induktives Aluminiumlöten wird in der Industrie immer häufiger eingesetzt. Ein typisches Beispiel ist das Hartlöten verschiedener Rohre an einem Wärmetauschergehäuse für Kraftfahrzeuge. Die Induktionsheizspule Die für diese Art von Verfahren am häufigsten verwendete Spule ist die nicht umlaufende Spule, die auch als "Hufeisen-Haarnadel"-Spule bezeichnet werden kann. Bei diesen Spulen sind das Magnetfeld und die daraus resultierende Wirbelstromverteilung von Natur aus dreidimensional. Bei diesen Anwendungen gibt es Probleme mit der Verbindungsqualität und der Konsistenz der Ergebnisse von Teil zu Teil. Um ein solches Problem für einen großen Automobilhersteller zu lösen, wurde das Computersimulationsprogramm Flux3D für die Prozessstudie und -optimierung eingesetzt. Die Optimierung umfasste eine Änderung der Konfiguration der Induktionsspule und des Magnetflussreglers. Mit den neuen Induktionsspulen, die in einem Labor experimentell validiert wurden, werden an mehreren Produktionsstandorten Teile mit höherer Verbindungsqualität hergestellt.
Jedes Auto benötigt mehrere verschiedene Wärmetauscher (Heizkörper, Verdampfer, Kondensatoren, Kühler usw.) für die Kühlung des Antriebsstrangs, der Klimaanlage, der Ölkühlung usw. Die überwiegende Mehrheit der Wärmetauscher von Personenkraftwagen wird heute aus Aluminium oder Aluminiumlegierungen hergestellt. Selbst wenn derselbe Motor für mehrere Automodelle verwendet wird, können die Anschlüsse aufgrund unterschiedlicher Layouts unter der Motorhaube variieren. Aus diesem Grund ist es gängige Praxis der Teilehersteller, mehrere Grundkörper für Wärmetauscher herzustellen und dann in einem zweiten Arbeitsgang verschiedene Anschlüsse anzubringen.
Wärmetauschergehäuse bestehen in der Regel aus Aluminiumlamellen, -rohren und -sammlern, die in einem Ofen zusammengelötet werden. Nach dem Löten werden die Wärmetauscher an das jeweilige Fahrzeugmodell angepasst, indem entweder Nylontanks oder - am häufigsten - verschiedene Aluminiumrohre mit Anschlussblöcken angebracht werden. Diese Rohre werden entweder durch MIG-Schweißen, Flamm- oder Induktionslöten miteinander verbunden. Beim Hartlöten ist aufgrund des geringen Unterschieds zwischen der Schmelz- und der Löttemperatur von Aluminium (20-50 °C je nach Legierung, Zusatzwerkstoff und Atmosphäre), der hohen Wärmeleitfähigkeit von Aluminium und der geringen Entfernung zu anderen, in einem früheren Arbeitsgang gelöteten Verbindungen eine sehr genaue Temperaturkontrolle erforderlich.
Induktionserwärmung ist eine gängige Methode zum Hartlöten verschiedener Rohre an Wärmetauschersammlern. Abbildung 1 ist ein Bild einer Induktionslöten Einrichtung zum Löten eines Rohrs an ein Rohr in einem Wärmetauschersammler. Aufgrund der Anforderungen an eine präzise Erwärmung muss sich die Fläche der Induktionsspule in unmittelbarer Nähe der zu lötenden Verbindung befinden. Daher kann eine einfache zylindrische Spule nicht verwendet werden, da das Teil nach dem Löten nicht mehr entfernt werden kann.
Es gibt zwei Haupttypen von Induktionsspulen, die für das Löten dieser Verbindungen verwendet werden: "Muschel"- und "Hufeisen-Haarnadel"-Induktoren. Die "Clamshell"-Induktoren ähneln den zylindrischen Induktoren, lassen sich jedoch öffnen, um die Entnahme von Teilen zu ermöglichen. "Horseshoe-Hairpin"-Induktoren haben die Form eines Hufeisens zum Laden des Teils und bestehen im Wesentlichen aus zwei Haarnadelspulen auf gegenüberliegenden Seiten der Verbindung.
Der Vorteil eines "Clamshell"-Induktors besteht darin, dass die Erwärmung über den gesamten Umfang gleichmäßiger ist und sich relativ leicht vorhersagen lässt. Der Nachteil eines "Clamshell"-Induktors ist, dass das erforderliche mechanische System komplizierter ist und die Hochstromkontakte relativ unzuverlässig sind.
"Hufeisen-Haarnadel"-Induktoren erzeugen kompliziertere 3D-Wärmemuster als "Clamshells". Der Vorteil eines "Hufeisen-Haarnadel"-Induktors ist, dass die Handhabung der Teile vereinfacht wird.
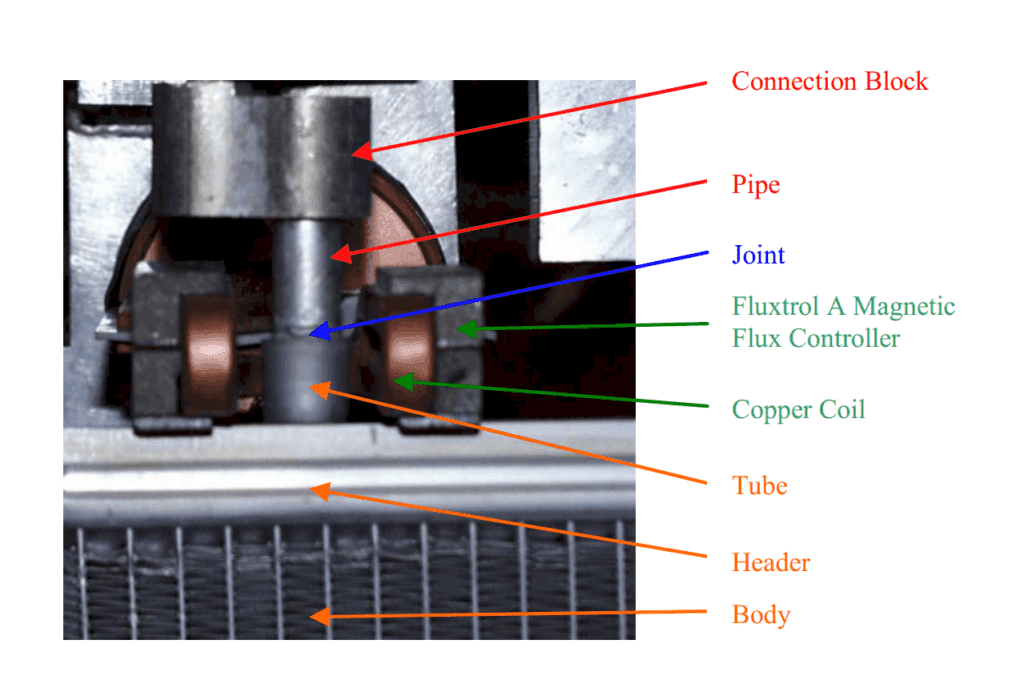
Computersimulation optimiert das Hartlöten
Ein großer Hersteller von Wärmetauschern hatte Qualitätsprobleme beim Löten der in Abb. 1 gezeigten Verbindung mit einem hufeisenförmigen Induktor. Die Lötverbindung war für die meisten Teile gut, aber die Erwärmung verlief bei einigen Teilen völlig anders, was zu einer unzureichenden Verbindungstiefe, kalten Verbindungen und durch lokale Überhitzung an der Rohrwand hochlaufendem Zusatzmetall führte. Selbst nach der Prüfung jedes Wärmetauschers auf Leckagen waren einige Teile an dieser Verbindung im Betrieb undicht. Das Centre for Induction Technology Inc. wurde damit beauftragt, das Problem zu analysieren und zu lösen.
Die für diese Aufgabe verwendete Stromversorgung hat eine variable Frequenz von 10 bis 25 kHz und eine Nennleistung von 60 kW. Beim Lötprozess bringt ein Bediener einen Schweißring am Rohrende an und führt das Rohr in die Röhre ein. Ein Wärmetauscher wird auf eine spezielle Vorrichtung gesetzt und in den Hufeiseninduktor geschoben.
Der gesamte Lötbereich wird vorgeflutet. Die Frequenz, mit der das Teil erwärmt wird, beträgt in der Regel 12 bis 15 kHz, und die Erwärmungszeit beträgt etwa 20 Sekunden. Die Leistung ist so programmiert, dass sie am Ende des Heizzyklus linear abnimmt. Ein optisches Pyrometer schaltet die Leistung ab, wenn die Temperatur auf der Rückseite der Verbindung einen voreingestellten Wert erreicht.
Es gibt viele Faktoren, die zu den vom Hersteller festgestellten Unstimmigkeiten führen können, wie z. B. Abweichungen bei den Verbindungselementen (Abmessungen und Position) sowie instabiler und (zeitlich) variabler elektrischer und thermischer Kontakt zwischen dem Rohr, der Leitung, dem Einfüllring usw. Einige Phänomene sind von Natur aus instabil, und kleine Variationen dieser Faktoren können eine unterschiedliche Prozessdynamik verursachen. So kann sich beispielsweise der offene Schweißzusatzring unter den elektromagnetischen Kräften teilweise abwickeln, und das freie Ende des Rings kann durch Kapillarkräfte zurückgesaugt werden oder ungeschmolzen bleiben. Diese Störfaktoren lassen sich nur schwer reduzieren oder beseitigen, und die Lösung des Problems erfordert eine Erhöhung der Robustheit des gesamten Prozesses. Die Computersimulation ist ein wirksames Instrument zur Analyse und Optimierung des Prozesses.
Bei der Bewertung des Lötvorgangs wurden starke elektrodynamische Kräfte beobachtet. In dem Moment, in dem der Strom eingeschaltet wird, erfährt die Hufeisenspule eindeutig eine Ausdehnung aufgrund einer plötzlichen Anwendung der elektrodynamischen Kraft. Daher wurde der Induktor mechanisch verstärkt, u. a. durch den Einbau einer zusätzlichen Glasfaserplatte (G10), die die Wurzeln der beiden Haarnadelspulen verbindet. Ein weiterer Beweis für die vorhandenen elektrodynamischen Kräfte war die Verlagerung des geschmolzenen Zusatzmetalls weg von den Bereichen in der Nähe der Kupferwindungen, wo das Magnetfeld stärker ist. Bei einem normalen Prozess verteilt sich der Schweißzusatz aufgrund der Kapillarkräfte und der Schwerkraft gleichmäßig um die Verbindung, während bei einem anormalen Prozess der Schweißzusatz aus der Verbindung herauslaufen oder sich entlang der Rohroberfläche nach oben bewegen kann.
Denn Induktionslöten von Aluminium ein sehr komplizierter Prozess ist, kann man keine genaue Simulation der gesamten Kette von miteinander gekoppelten Phänomenen (elektromagnetisch, thermisch, mechanisch, hydrodynamisch und metallurgisch) erwarten. Der wichtigste und am besten kontrollierbare Prozess ist die Erzeugung elektromagnetischer Wärmequellen, die mit dem Programm Flux 3D analysiert wurden. Aufgrund der Komplexität des Induktionslötprozesses wurde für die Prozessgestaltung und -optimierung eine Kombination aus Computersimulation und Experimenten verwendet.