コンピュータ支援による誘導アルミニウムろう付け
誘導アルミニウムろう付け は、産業界でますます一般的になってきている。典型的な例は、自動車用熱交換器のボディにさまざまなパイプをろう付けすることだ。その 誘導加熱コイル この種のプロセスに広く使われているのは、「ホースシュー・ヘアピン」スタイルと呼ばれる非周回型のものである。これらのコイルでは、磁場とその結果生じる渦電流分布は本質的に3次元的なものである。このような用途では、接合部の品質や部品ごとの結果の一貫性に問題があります。ある大手自動車メーカーがこのような問題を解決するために、FLUX3Dコンピュータシミュレーショ ンプログラムをプロセスの検討と最適化に使用しました。最適化には、誘導コイルと磁束コントローラーの構成の変更が含まれました。実験室で検証された新しい誘導コイルは、複数の生産拠点でより高品質の接合部を持つ部品を生産しています。
各車両は、パワートレイン冷却、エアコン、オイル冷却などのために、数種類の熱交換器(ヒーターコア、エバポレーター、コンデンサー、ラジエーターなど)を必要とします。今日の乗用車用熱交換器の大部分は、アルミニウムまたはアルミニウム合金製です。同じエンジンが複数の自動車モデルに使用されている場合でも、ボンネット内のレイアウトが異なるため、接続部が異なることがあります。このため、部品メーカーは基本的な熱交換器本体をいくつか作り、二次加工で異なるコネクターを取り付けるのが標準的な方法です。
熱交換器の本体は通常、アルミニウムのフィン、チューブ、ヘッダーを炉でろう付けしたものである。ろう付け後、熱交換器は、ナイロンタンクか、最も一般的な接続ブロック付きの異なるアルミニウムパイプを取り付けることによって、指定された車種用にカスタマイズされる。これらのパイプは、MIG溶接、フレームまたは誘導ろう付けによって取り付けられる。ろう付けの場合、アルミニウムの溶解温度とろう付け温度の差が小さいこと(合金、ろう材、雰囲気によって20~50℃異なる)、アルミニウムの熱伝導率が高いこと、前の作業でろう付けされた他の接合部との距離が短いことから、非常に精密な温度制御が要求される。
誘導加熱 は、各種パイプを熱交換器のヘッダーにろう付けする一般的な方法である。図1は 誘導ろう付け 熱交換器ヘッダーのチューブにパイプをろう付けするためのセットアップ。正確な加熱が要求されるため、誘導コイルの面はろう付けされる接合部に近接していなければなりません。そのため、単純な円筒形コイルは、接合部のろう付け後に取り外すことができないため、使用できません。
これらの接合部のろう付けに使用される誘導コイルには、主に2つのスタイルがある:「クラムシェル型」と「馬蹄形ヘアピン型」です。「クラムシェル」インダクタは円筒形インダクタに似ていますが、部品の取り外しができるように開いています。「馬蹄形ヘアピン」インダクターは、部品に荷重をかけるために馬蹄のような形をしており、基本的にジョイントの反対側に2つのヘアピンコイルがあります。
クラムシェル "インダクターを使用する利点は、加熱が円周上でより均一であり、予測が比較的容易であることである。一方、「クラムシェル」インダクタの欠点は、必要な機械システムがより複雑であることと、大電流接点が比較的信頼性に欠けることである。
「馬蹄形ヘアピン」インダクターは「クラムシェル」よりも複雑な3次元ヒートパターンを生成する。ホースシューヘアピン型インダクタの利点は、部品の取り扱いが簡素化されることです。
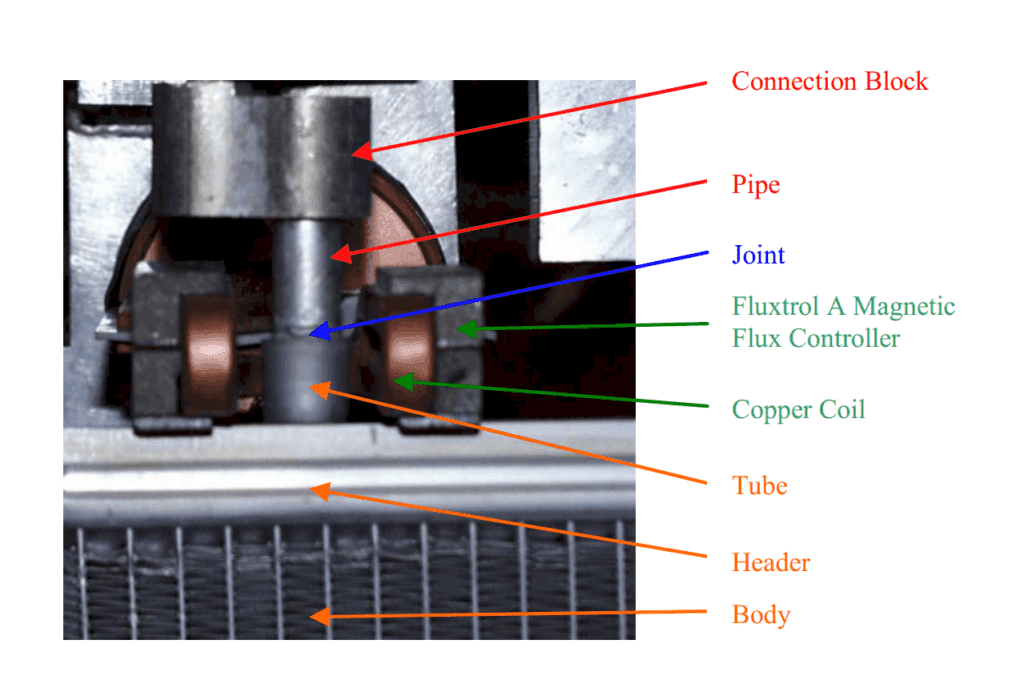
コンピュータ・シミュレーションによるろう付けの最適化
ある大手熱交換器メーカーは、馬蹄形ヘアピン型インダクターを使用した図1に示す接合部のろう付けに品質上の問題を抱えていた。大半の部品ではろう付け接合は良好でしたが、一部の部品では加熱がまったく異なるため、接合深さが不足したり、接合部が冷えたり、局所的な過熱によってろう材がパイプ壁を駆け上がったりしていました。各熱交換器の漏れを検査しても、使用中にこの接合部から漏れる部品もありました。センター・フォー・インダクション・テクノロジー社は、この問題の分析と解決を請け負った。
この作業に使用される電源の周波数は10~25 kHzの可変周波数で、定格出力は60 kWである。ろう付け工程では、オペレーターがパイプの端にろうリングを取り付け、パイプを管内に挿入する。熱交換器が特別なリグに設置され、馬蹄形インダクター内を移動する。
ろう付け領域全体がプリフラックスされる。部品の加熱に使用される周波数は通常12~15 kHzで、加熱時間は約20秒である。電力レベルは、加熱サイクルの終了時に直線的に減少するようにプログラムされている。光学式パイロメーターは、接合部裏面の温度があらかじめ設定された値に達すると電源を切ります。
このメーカーが経験していたような不一致を引き起こす可能性のある要因は数多くある。例えば、接合部品(寸法や位置)のばらつきや、チューブ、パイプ、フィラーリングなどの間の電気的・熱的接触が不安定で(時間的に)変動しやすいことなどである。いくつかの現象は本質的に不安定であり、これらの要因のわずかな変動が、異なるプロセスダイナミクスを引き起こす可能性がある。例えば、開いたフィラーリングが電磁力によって部分的に巻き戻ったり、リングの自由端が毛細管力によって吸い戻されたり、溶けずに残ったりすることがある。このようなノイズ要因を低減または除去することは困難であり、この問題を解決するには、プロセス全体のロバスト性を高める必要があった。コンピュータ・シミュレーションは、プロセスを分析し最適化するための効果的なツールである。
ろう付けプロセスの評価中、強い電気力学的な力が観察された。電源が投入された瞬間、馬蹄形コイルは電気力学的な力が急激に加わるため、明らかに膨張を経験する。そこで、2つのヘアピンコイルの根元をつなぐグラスファイバー(G10)プレートを追加するなどして、インダクタを機械的に強くした。電気力学的な力が存在することを示すもう一つの実証は、磁場がより強い銅ターンに近い領域から溶融金属フィラーが離れていくことでした。正常なプロセスでは、金属フィラーは毛細管力と重力によって接合部の周囲に均一に分布するが、異常なプロセスでは金属フィラーが接合部から流出したり、パイプ表面に沿って移動したりする。
なぜなら 誘導アルミニウムろう付け は非常に複雑なプロセスであり、相互に連関する現象(電磁、熱、機械、流体力学、冶金学)の連鎖全体を正確にシミュレーションすることは不可能である。最も重要で制御可能なプロセスは電磁熱源の発生であり、Flux 3Dプログラムを使って解析しました。誘導ろう付けプロセスは複雑なため、プロセスの設計と最適化にはコンピューターシミュレーションと実験を組み合わせた。