Brasatura dell'alluminio a induzione con assistenza computerizzata
Brasatura ad induzione dell'alluminio sta diventando sempre più comune nell'industria. Un esempio tipico è la brasatura di vari tubi sul corpo di uno scambiatore di calore automobilistico. Il bobina di riscaldamento a induzione La bobina più utilizzata per questo tipo di processo è quella non circolare, che può essere definita "a ferro di cavallo". Per queste bobine, il campo magnetico e la conseguente distribuzione di correnti parassite sono di natura tridimensionale. In queste applicazioni, esistono problemi di qualità dei giunti e di coerenza dei risultati da un pezzo all'altro. Per risolvere uno di questi problemi per un grande produttore automobilistico, è stato utilizzato il programma di simulazione al computer Flux3D per lo studio e l'ottimizzazione del processo. L'ottimizzazione comprendeva la modifica della configurazione della bobina di induzione e del controllore di flusso magnetico. Le nuove bobine di induzione, convalidate sperimentalmente in laboratorio, producono pezzi con giunti di qualità superiore in diversi siti produttivi.
Ogni auto richiede diversi scambiatori di calore (radiatori, evaporatori, condensatori, radiatori, ecc.) per il raffreddamento della trasmissione, dell'aria condizionata, dell'olio, ecc. La stragrande maggioranza degli scambiatori di calore delle autovetture è oggi realizzata in alluminio o in leghe di alluminio. Anche se lo stesso motore viene utilizzato per diversi modelli di automobili, i collegamenti possono variare a causa della diversa disposizione sotto il cofano. Per questo motivo, è prassi comune per i produttori di componenti realizzare diversi corpi di base per gli scambiatori di calore e poi applicare connettori diversi in un'operazione secondaria.
I corpi degli scambiatori di calore sono solitamente costituiti da alette, tubi e testate in alluminio brasati insieme in un forno. Dopo la brasatura, gli scambiatori di calore vengono personalizzati per il modello di auto in questione, collegando serbatoi in nylon o, più comunemente, diversi tubi in alluminio con blocchi di connessione. Questi tubi vengono fissati mediante saldatura MIG, brasatura a fiamma o a induzione. Nel caso della brasatura, è necessario un controllo molto preciso della temperatura a causa della piccola differenza tra le temperature di fusione e brasatura dell'alluminio (20-50 C a seconda della lega, del metallo d'apporto e dell'atmosfera), dell'elevata conducibilità termica dell'alluminio e della breve distanza da altri giunti brasati in un'operazione precedente.
Riscaldamento a induzione è un metodo comune per brasare vari tubi alle testate degli scambiatori di calore. La Figura 1 mostra un'immagine di un brasatura a induzione per la brasatura di un tubo su una testata di uno scambiatore di calore. A causa dei requisiti di precisione del riscaldamento, la faccia della bobina a induzione deve essere in prossimità del giunto da brasare. Pertanto, non è possibile utilizzare una semplice bobina cilindrica, in quanto la parte non può essere rimossa dopo la brasatura del giunto.
Esistono due tipi principali di bobine a induzione utilizzate per la brasatura di questi giunti: Gli induttori "a conchiglia" e quelli "a ferro di cavallo". Gli induttori "a conchiglia" sono simili agli induttori cilindrici, ma si aprono per consentire la rimozione dei pezzi. Gli induttori "a ferro di cavallo" hanno la forma di un ferro di cavallo per caricare il pezzo e sono essenzialmente due bobine a forcina sui lati opposti del giunto.
Il vantaggio di utilizzare un induttore "a conchiglia" è che il riscaldamento è più uniforme sulla circonferenza e relativamente facile da prevedere. Lo svantaggio di un induttore "Clamshell" è che il sistema meccanico richiesto è più complicato e i contatti ad alta corrente sono relativamente inaffidabili.
Gli induttori a "ferro di cavallo" producono schemi termici tridimensionali più complicati rispetto ai "Clamshell". Il vantaggio di un induttore a "ferro di cavallo" è che la gestione dei pezzi è semplificata.
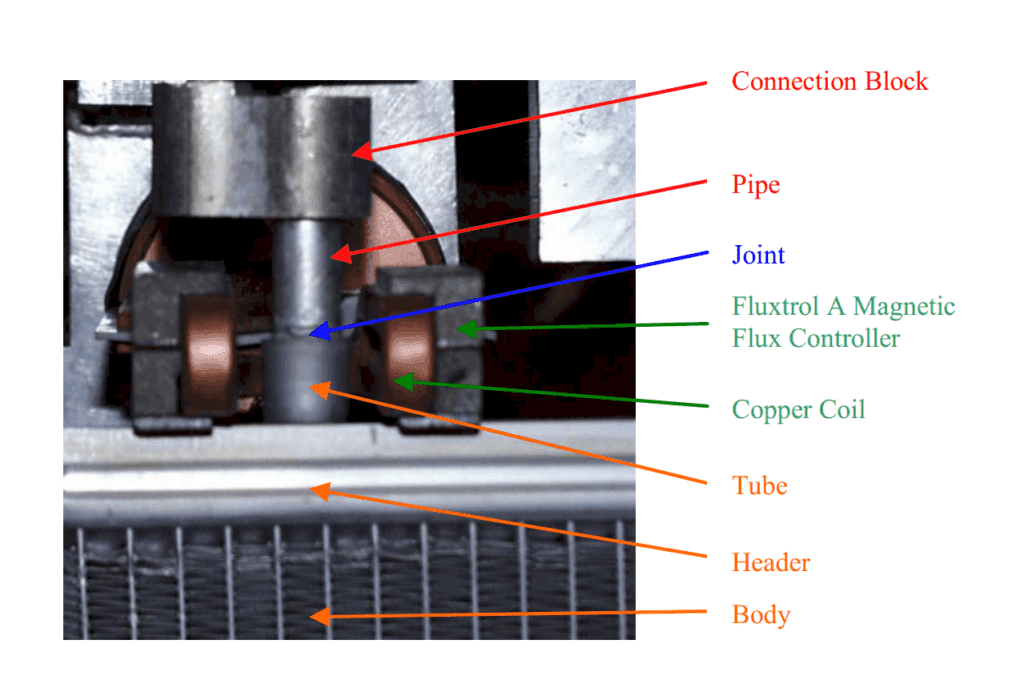
La simulazione al computer ottimizza la brasatura
Un grande produttore di scambiatori di calore aveva problemi di qualità con la brasatura del giunto mostrato nella Fig. 1, utilizzando un induttore a ferro di cavallo. Il giunto di brasatura era buono per la maggior parte dei pezzi, ma il riscaldamento era completamente diverso per alcuni pezzi, con conseguente profondità insufficiente del giunto, giunti freddi e metallo d'apporto che risaliva la parete del tubo a causa del surriscaldamento locale. Anche dopo aver testato ogni scambiatore di calore per verificare la presenza di perdite, alcune parti continuavano a perdere in corrispondenza di questo giunto durante il servizio. Il Centre for Induction Technology Inc. è stato incaricato di analizzare e risolvere il problema.
L'alimentatore utilizzato per il lavoro ha una frequenza variabile da 10 a 25 kHz e una potenza nominale di 60 kW. Nel processo di brasatura, un operatore installa un anello di metallo di riempimento sull'estremità del tubo e inserisce il tubo all'interno del tubo. Uno scambiatore di calore viene posizionato su uno speciale impianto e spostato all'interno dell'induttore a ferro di cavallo.
L'intera area di brasatura è preflussata. La frequenza utilizzata per riscaldare il pezzo è in genere compresa tra 12 e 15 kHz e il tempo di riscaldamento è di circa 20 secondi. Il livello di potenza è programmato con una riduzione lineare alla fine del ciclo di riscaldamento. Un pirometro ottico spegne la potenza quando la temperatura sul lato posteriore del giunto raggiunge un valore predefinito.
Sono molti i fattori che possono causare l'incoerenza riscontrata dal produttore, come la variazione dei componenti del giunto (dimensioni e posizione) e il contatto elettrico e termico instabile e variabile (nel tempo) tra tubo, tubazione, anello di riempimento, ecc. Alcuni fenomeni sono intrinsecamente instabili e piccole variazioni di questi fattori possono causare dinamiche di processo diverse. Ad esempio, l'anello di metallo d'apporto aperto può parzialmente srotolarsi sotto le forze elettromagnetiche e l'estremità libera dell'anello può essere risucchiata da forze capillari o rimanere non fusa. I fattori di disturbo sono difficili da ridurre o eliminare e la soluzione al problema richiedeva di aumentare la robustezza del processo complessivo. La simulazione al computer è uno strumento efficace per analizzare e ottimizzare il processo.
Durante la valutazione del processo di brasatura, sono state osservate forti forze elettrodinamiche. Al momento dell'accensione, la bobina a ferro di cavallo subisce chiaramente un'espansione dovuta all'improvvisa applicazione della forza elettrodinamica. Per questo motivo, l'induttore è stato reso meccanicamente più forte, incorporando anche una piastra aggiuntiva in fibra di vetro (G10) che collega le radici di due bobine a forcina. L'altra dimostrazione della presenza di forze elettrodinamiche è stata lo spostamento del metallo d'apporto fuso dalle aree vicine alle spire di rame, dove il campo magnetico è più forte. In un processo normale, il metallo d'apporto si distribuisce uniformemente intorno al giunto grazie alle forze capillari e alla gravità, mentre in un processo anomalo il metallo d'apporto può fuoriuscire dal giunto o risalire lungo la superficie del tubo.
Perché brasatura ad induzione dell'alluminio è un processo molto complicato, non è possibile aspettarsi una simulazione accurata dell'intera catena di fenomeni reciprocamente accoppiati (elettromagnetici, termici, meccanici, idrodinamici e metallurgici). Il processo più importante e controllabile è la generazione di fonti di calore elettromagnetiche, che sono state analizzate con il programma Flux 3D. Data la natura complessa del processo di brasatura a induzione, per la progettazione e l'ottimizzazione del processo è stata utilizzata una combinazione di simulazione al computer ed esperimenti.
Brasatura_ad_induzione_di_alluminio_con_assistenza_al_computer